
„He who stops being better stops being good“
(Oliver Cromwell)
iMAR Navigation GmbH
is a worldwide leading provider of systems and solutions in inertial navigation, stabilization, guidance and control for all industrial, automotive, geodetic, aviation, surveying as well as defence applications and sovereign tasks.
iMAR Navigation GmbH, a German company, is a well-known specialist and innovator in leading inertial systems and solutions for more than 30 years. With our extensive long-time experience in production, development, maintenance and support of inertial systems for positioning, navigation, surveying, guidance, stabilization, control and communication (PNT / PNTC) we provide leading systems and solutions destined to a wide range of applications, for unmanned and manned platforms, in industrial, automotive, aerospace, geodetic and defence environment, from stock or as customized solution.
A solid foundation for the manufacturing and development of reliable inertial measurement systems and solutions is formed by our comprehensive expertise in the fields of inertial measurement technology, navigation algorithms, sensors, real-time signal processing, and sensor-proximate hardware design. Furthermore, we can draw upon over 30 years of experience in integration engineering across all application areas for our clients, in-house development and production, and a market-leading field experience with inertial measurement systems encompassing nearly all sensor technologies.
iMAR operates an advanced and powerful in-house manufacturing and integration infrastructure: Several multi axes turntables and temperature lab, vibration and shock testing lab, a hexapod 6D high dynamic motion simulator for up to 1 ton payload, 3-axes and 5 axes CNC machine tools, ZEISS coordinate measuring machine etc.; click on the picture to have a look into one of iMAR's manufacturing and integration labs.
iMAR Navigation was founded in 1992 and is located in St. Ingbert, near Frankfurt (Germany), where it has its headquarters, its engineering site and production site (3'100 sq.m / 34'000 sq.ft).
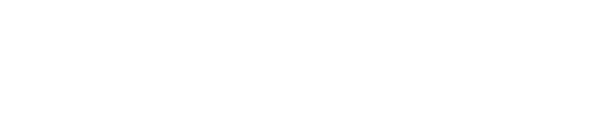
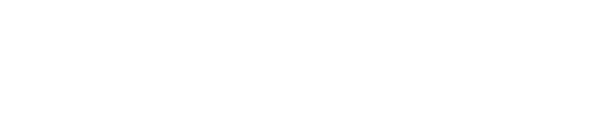
Why choose iMAR ?
For more than 30 years we provide successful solutions and intergation engineering for nearly all fields in the area of inertial navigation, localization, guidance & control.
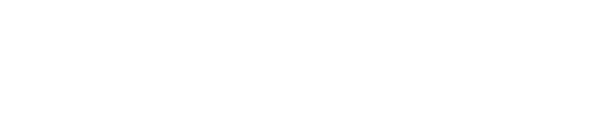
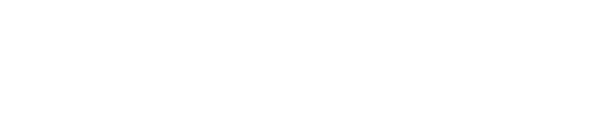
Why choose iMAR ?
Extensive practical experience with all commonly used inertial sensor technologies.
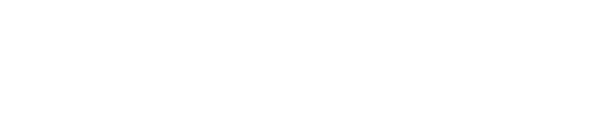
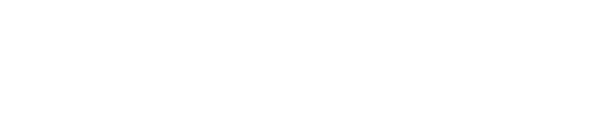
Why choose iMAR ?
Only physics determines the behavior of iMAR‘s measurement systems. Our real-time output of our systems and solutions is achieved through the intelligent signal processing invented by our experienced engineers - and not by AI.
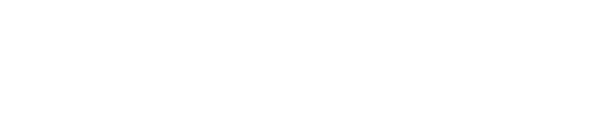
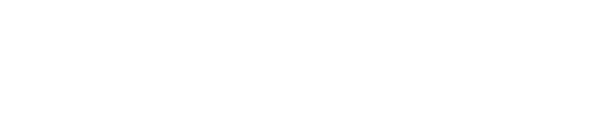
Why choose iMAR ?
Leading integrators and users of inertial solutions recommend not to entrust the success of critical or general missions to the heuristic decisions of any AI (artificial intelligence). iMAR provides highest reliability, accuracy and availability of inertial solutions based on our leading knowledge in mathematics, physics and system design.
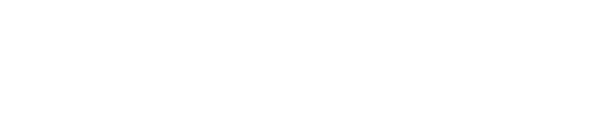
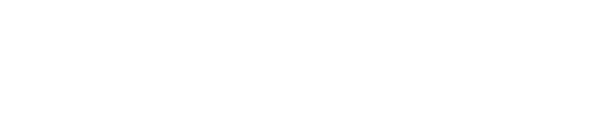
Why choose iMAR ?
Exceptional flexibility for the benefit of our customers through in-house development of hardware, software, firmware, algorithms, and system manufacturing.
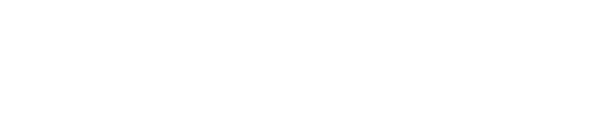
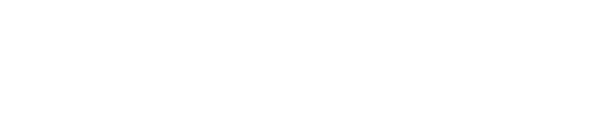
Why choose iMAR ?
We deliver products of the highest reliability, accuracy, and robustness - Made in Germany.
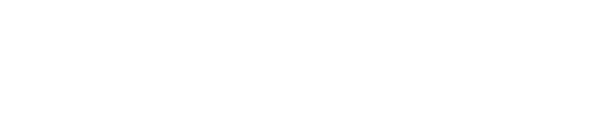
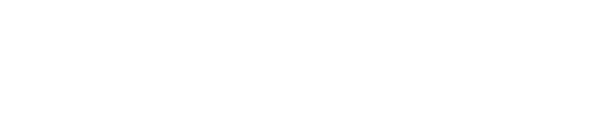
Why choose iMAR ?
Our in-house environmental test lab, including our facilities for temperature, vibration, shock, and motion, as well as our according ISO 17025 DAkkS accredidated EMI/EMC testing facilities, qualifies our products according to the relevant military, railway, space and aviation standards.
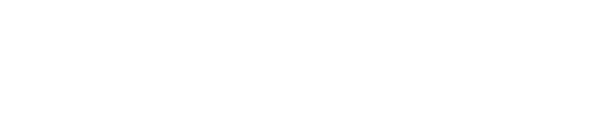
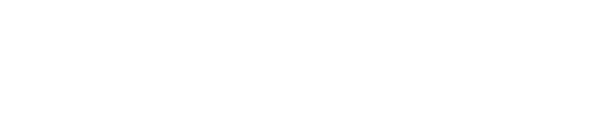
Why choose iMAR ?
iMAR's design and manufacturing processes are certified according to EN 9100, ISO 9001. Furthermore, iMAR is certified by the German Federal Aviation Office (LBA) in accordance with EASA Part 21G (approval for aviation equipment manufacturing). Also iMAR's Safety Management System (SMS) is certified by LBA / EASA. This assures highest quality standards at iMAR.
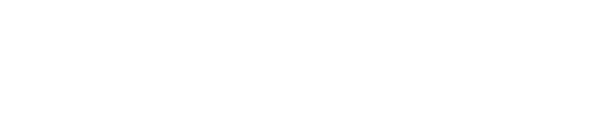
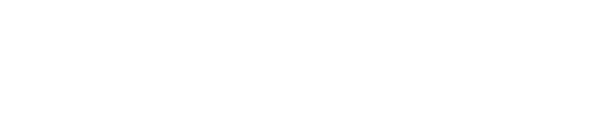
Why iMAR ?
In addition to our standard products, we provide custom solutions tailored to your requirements, from single units, including training, to large quantities.
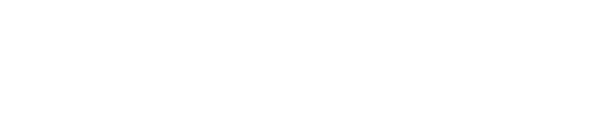
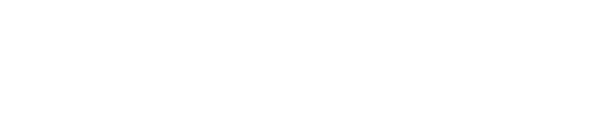
Why choose iMAR ?
We deliver the technically and economically best solution for your task with the most suitable sensor technology, electronics, and signal processing tailored to your specific needs.
The manufacturing includes series devices and system solutions, i.e. Commercial-off-the-Shelf (COTS) and Military-off-the-Shelf (MOTS), as well as customized solutions from the prototype over pre-series devices up to large quantities.
Three key elements make a sound basis for manufacturing and developing our advanced inertial measuring systems and solutions and bringing them into your application:
-
Our know-how with more than 30 years of expertise and field experience and in-depth knowledge of inertial measuring technologies, navigation algorithms, sensor systems, signal processing and mechatronics systems.
-
Our superior knowledge in hardware design, firmware design and software engineering including highly sophisticated sensor data fusion, including an aviation certified quality management.
-
Our strong support team, which is here to assist you, whether you are an experienced or less experienced user, in the successful integration and usage of our inertial systems into your application.
Our cost-effective, premium high-tech products and system solutions are the result of a policy of continuous investment in human resources and technological innovation - about 85 engineers and technicians, quality assurance and administration staff, all highly qualified and dedicated to their work, the availability of all state-of-the-art inertial sensor tech nologies ranging from MEMS gyros to hemispheric resonator gyros (HRG) and from fiber optic gyroscopes (FOG) to ring laser gyros (RLG), augmented by satellite, stereo vision and other technologies and a powerful development and production tool chain also featuring in-house Matlab/Simulink, SolidWorks, EDA tools, HyperMill, 3-axes and 5-axes CNC centres and much more.
iMAR operates extensive in-house manufacturing facilities. iMAR is manufacturing according to military, industrial, automotive and aerospace quality standards. The reliability of our products is guaranteed by our modern production site, which is certified according to ISO 9001 / EN 9100 quality standards (industrial engineering / development and production lifecycle according to aviation requirements). The production facility is certified to EASA Part21G (avionics equipment) since 09/2011.
iMAR's comprehensive in-house testing equipment also includes several two and three axes turntables, a micron accurate coordinate measuring machine, several full range temperature chambers, a 6 DOF hexapod motion simulator with up to +/-1 g acceleration and up to 1 ton payload, an advanced GNSS real-time simulator (incl. multi-constellation and RTK), and a 40 kN vibration and shock testing platform, also fully complying with mil/space specifications. Furthermore iMAR's daughter company Spezial-EMV GmbH operates a sophisticated EMI/EMC lab, which is accredidated by DAkkS according to ISO 17025.. After manufacturing, calibration and final testing, our products are delivered to customers operating them in industrial branches, automotive industry, in transportation and railway applications, in commercial, civil and military aviation, at the armed forces (navy, army and airforces) at special forces of many countries worldwide.
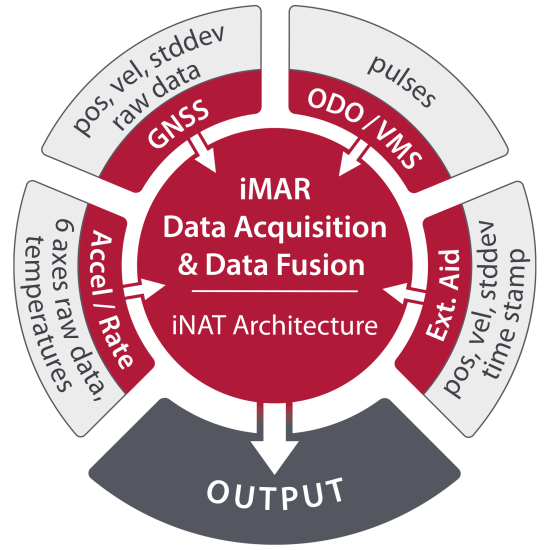
iNAT Architecture
iNAT: System Architecture Overview of all iNAT Systems (iMAR Navigation & Timing)
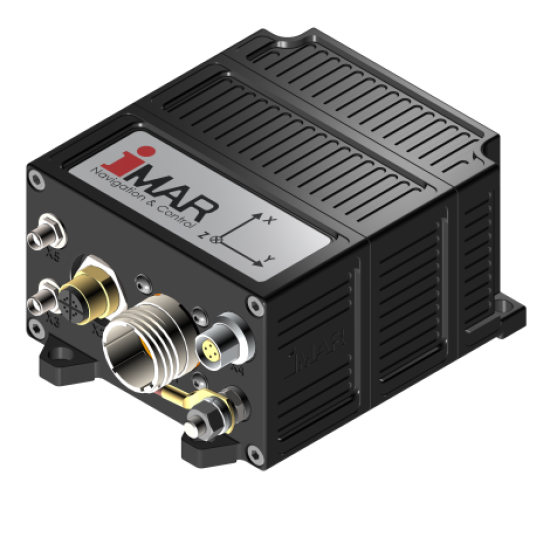
iNAT-M300 INS/GNSS Solution
Light weight INS/GNSS/ODO solutions for manned and unmanned applications: Position, velocity, attitude, heading, angular rates and acceleration of land vehicles, ships, aircrafts, naval and subsea vessels, missiles, mobile robots etc. for industrial, surveying, defense, transportation and research applications. Designed and qualified according to MIL standards (vibration, shock, temperature, EMI/EMC, humidity, altitude, salt & dust, fungus, acceleration).
The device is suitable also for critical missions and does not contain any AI based components.
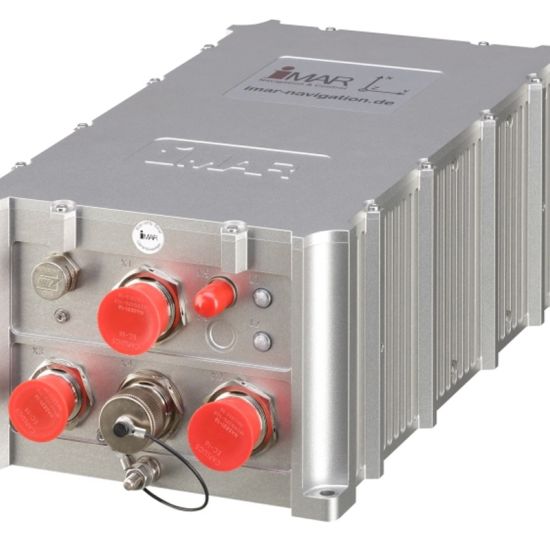
iNAT-RQx, iNAT-FSx, iNAT-MSx
Advanced INS/GNSS Systems for Navigation, Stabilization, Surveying, Guidance & Control for industrial, surveying, defense and research applications.
Designed and qualified according to MIL standards (vibration, shock, temperature, EMI/EMC, humidity, altitude, salt & dust, fungus, acceleration).
The device is suitable also for critical missions and does not contain any AI based components.
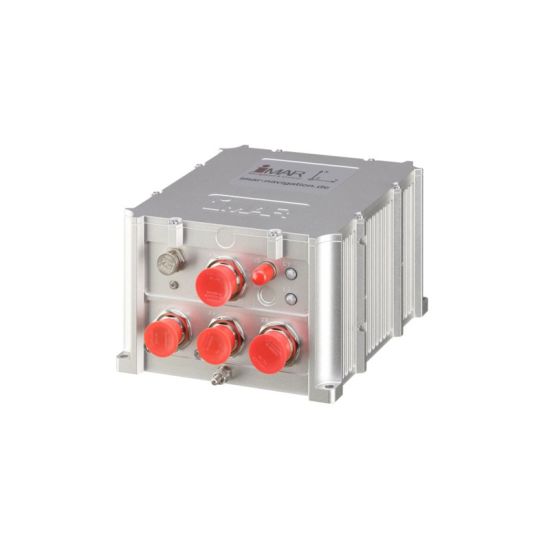
iNAT-FSLG / iTraceRT-MVT-510
Advanced INS/GNSS system to provide position, velocity, attitude, true heading, anglar rate and acceleration for Land, Air and Sea Applications.
Designed and qualified according to MIL standards (vibration, shock, temperature, EMI/EMC, humidity, altitude, salt & dust, fungus, acceleration).
The device is suitable also for critical missions and does not contain any AI based components.
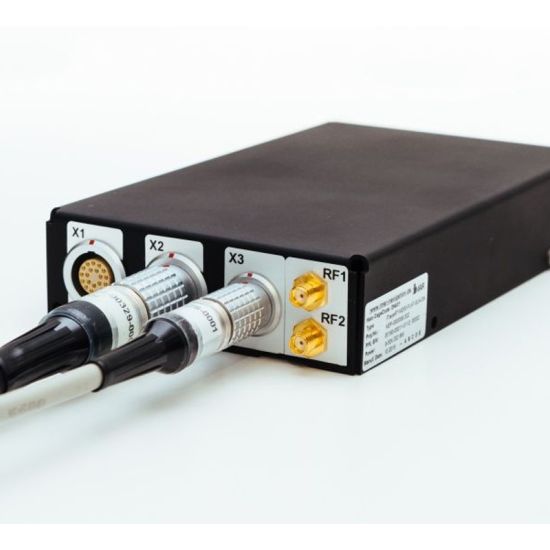
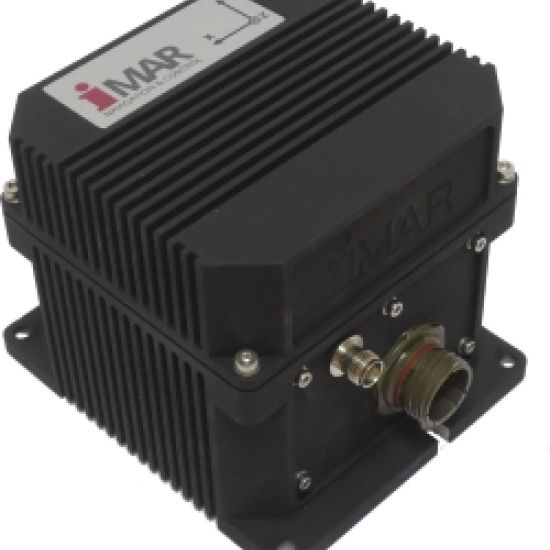
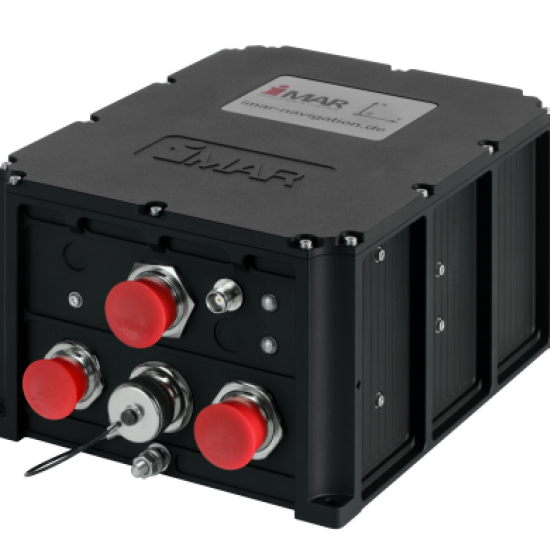
General Navigation and Surveying
Advanced navigation, localization, guidance and control system for industrial, defense, automotive, transportation, surveying and research applications (land, sea, subsea, air, space)
Designed and qualified according to MIL standards (vibration, shock, temperature, EMI/EMC, humidity, altitude, salt & dust, fungus, acceleration).
The device is suitable also for critical missions and does not contain any AI based components.
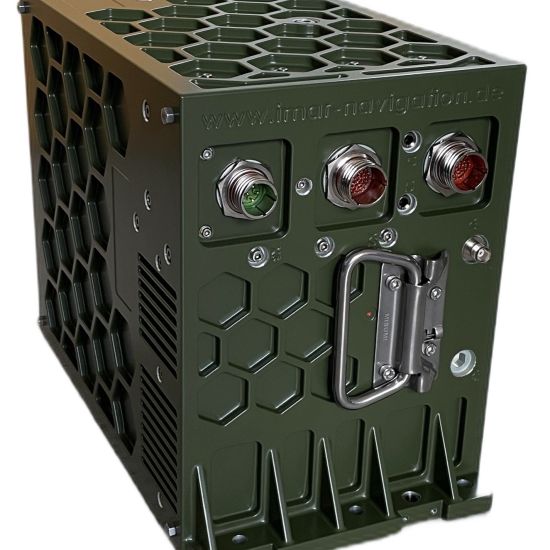
iPRENA-M
Most accurate inertial navigation system (INS/GNSS/VMS) with mechanical DRU/MAPS compatibility, used in the most challenging defence applications like radar systems and combat vehicles. The integrated ring laser gyro technolgy demonstrates in the daily operation its wellknown advantages upon other available technologies.
Designed and qualified according to MIL standards (vibration, shock, temperature, EMI/EMC, humidity, altitude, salt & dust, fungus, acceleration).
The device is suitable also for critical missions and does not contain any AI based components.
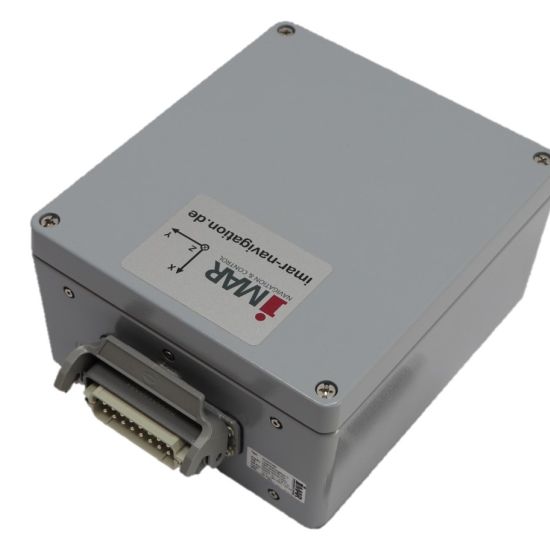
Railway Systems: iRailLoc-C, iRailLoc-R, iZET-Mobile
Systems for railway applications (localization, train integrity, ATO etc.).
Designed and qualified according to railway standards (vibration, shock, temperature, EMI/EMC, humidity, altitude, salt & dust, fungus, acceleration).
The device is suitable also for critical missions and does not contain any AI based components.
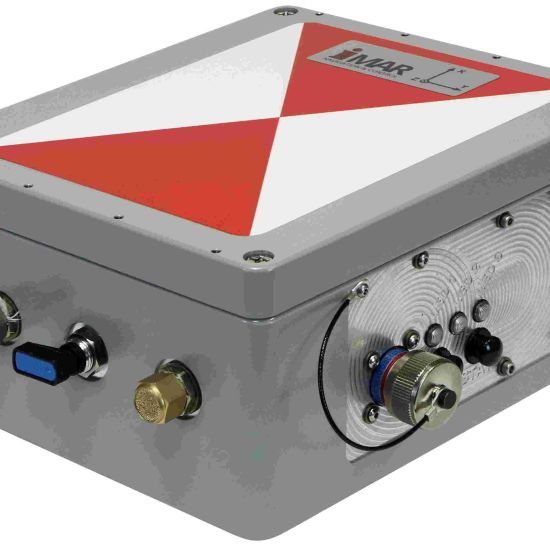
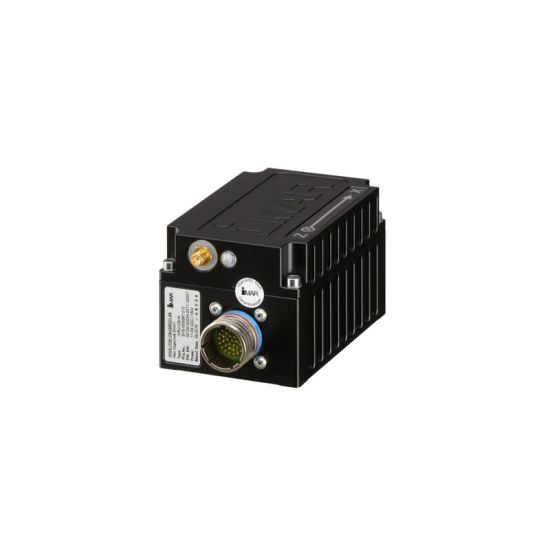
iNAT-CB-M and iVRU-CB-M
INS/GNSS Solutions for Target Drones and UAVs, Straddle Carriers and other automated vehicles (see also new generation iNAT-M300)
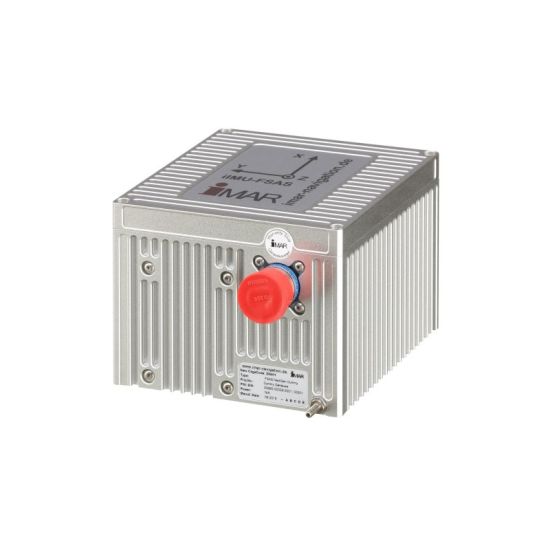
iIMU-FSAS
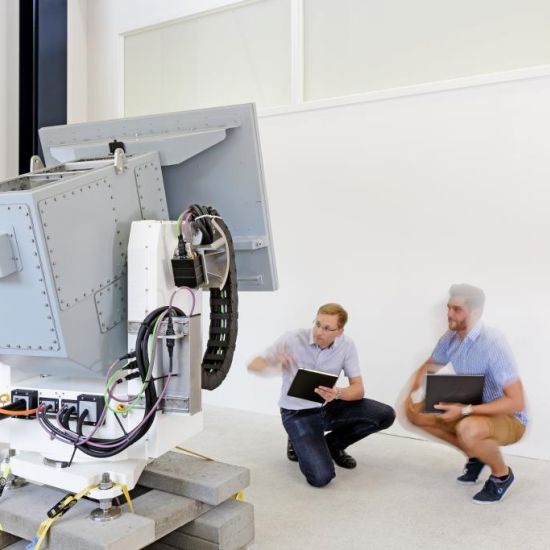
iIPSC-MSG
Gyro stabilized Gimbals for Antennas and EO/IR Payloads, standard designs and customized designs - from prototype to volume production.
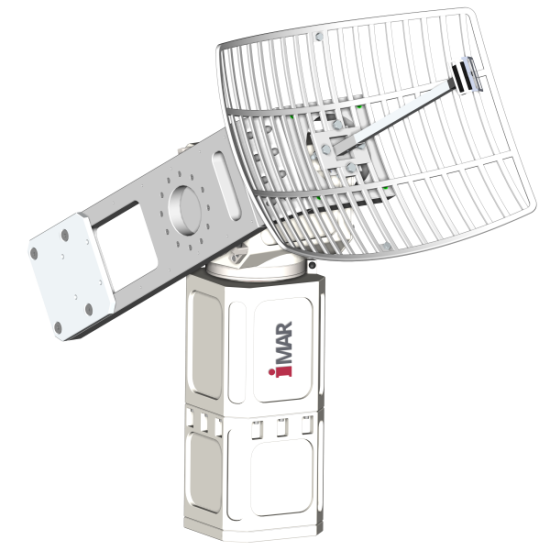
iIPSC-PT
iIPSC-PT is a leading gyro stabilized pan-tilt system for nearly arbitrary payloads, applcable on naval vessels, trucks etc.
Designed and qualified according to MIL standards (vibration, shock, temperature, EMI/EMC, humidity, altitude, salt & dust, fungus, acceleration).
The device is suitable also for critical missions and does not contain any AI based components.
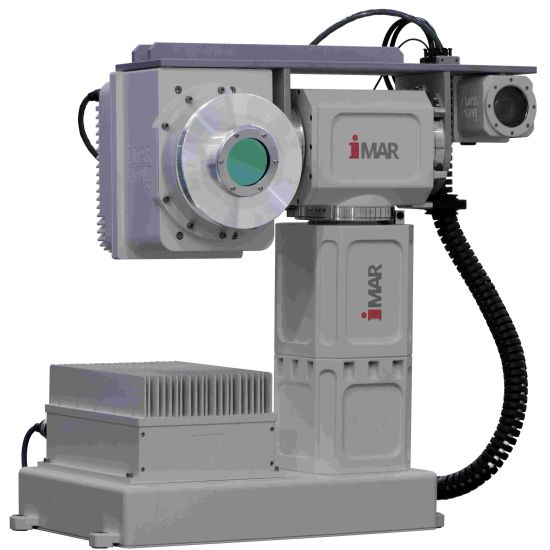
iIPSC-PT for EO/IR and antennas
iIPSC-PT is a leading gyro stabilized pan-tilt system for nearly arbitrary payloads, applcable on naval vessels, trucks etc.
Designed and qualified according to MIL standards (vibration, shock, temperature, EMI/EMC, humidity, altitude, salt & dust, fungus, acceleration).
The device is suitable also for critical missions and does not contain any AI based components.
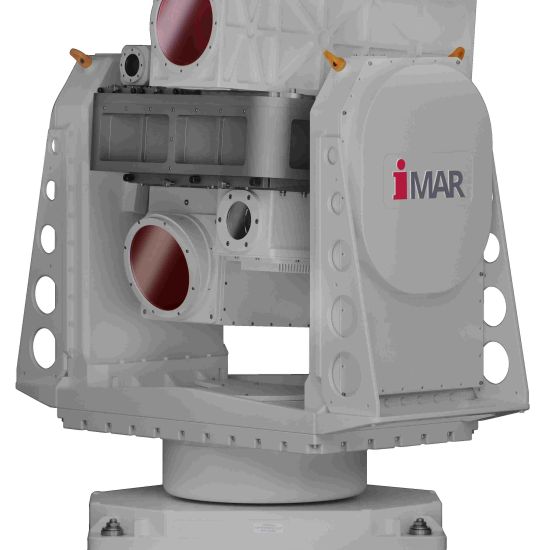
iIPSC-MSG Gryo Stabilized Gimbals
iIPSC-MSG: Gyro stabilized platforms to fulfill higest requirements in pointing, stabilization and tracking, for standard or custom specific payloads like EO/IR, antennas, lasers etc.
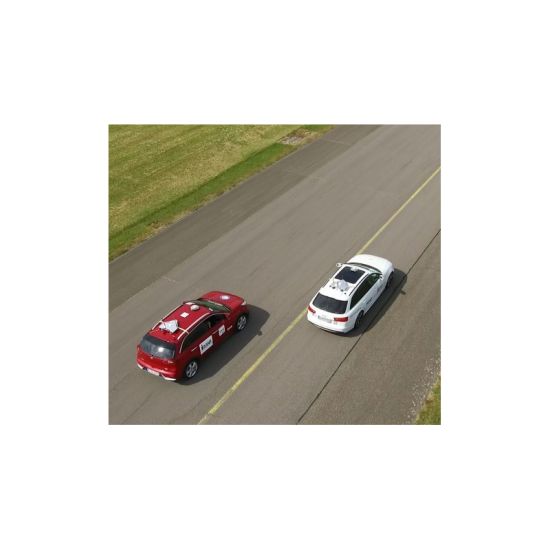
iSWACO-ARGUS - Automotive Testing
Proving ground instrumentation for testing self driving cars and trucks up to SAE level 5. Picture: Toolchain testing with PEGASUS approach, driving complex traffic scenarios and platooning. iMAR provides INS/GNSS/LiDAR based localization, trajectory planing and vehicle control. We also support in the instrumentation of communication infrastructure and RTK correction data.
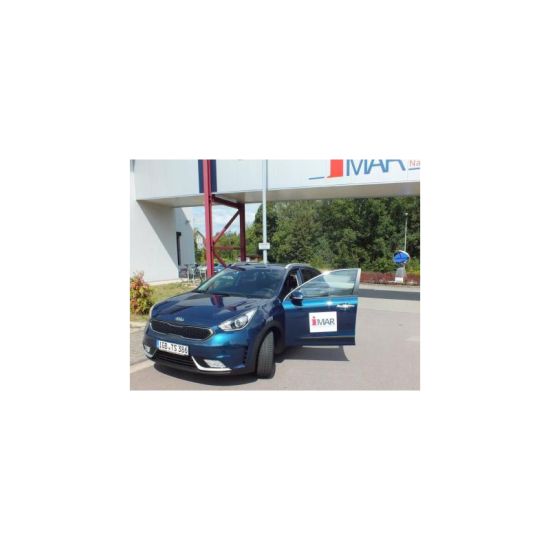
iTSV-KIA-NIRO
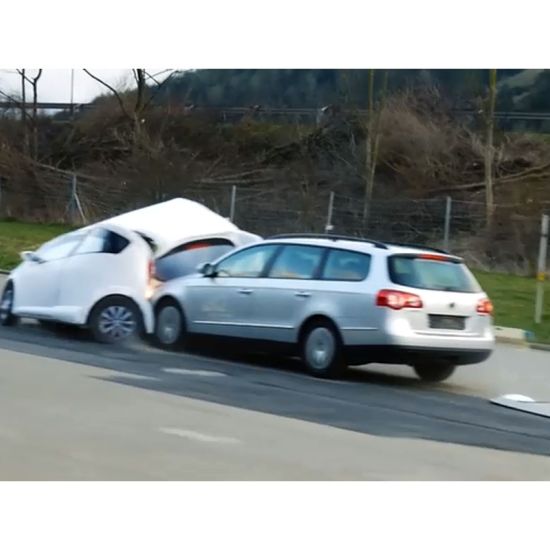
iSWACO-ARGUS - Automotive Testing
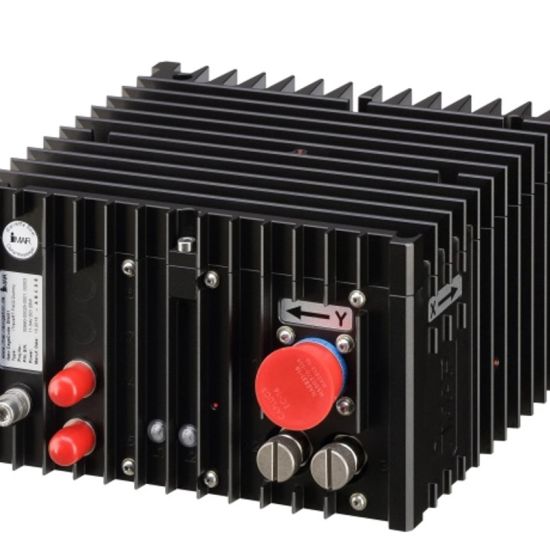
iTraceRT-F402/7
INS/GNSS based Motion Reference Systems for automotive testing until 2018. The successor is the iTraceRT-MVT system family, which covers the most accurate as well as the most economic solutions for automotive testing worldwide.
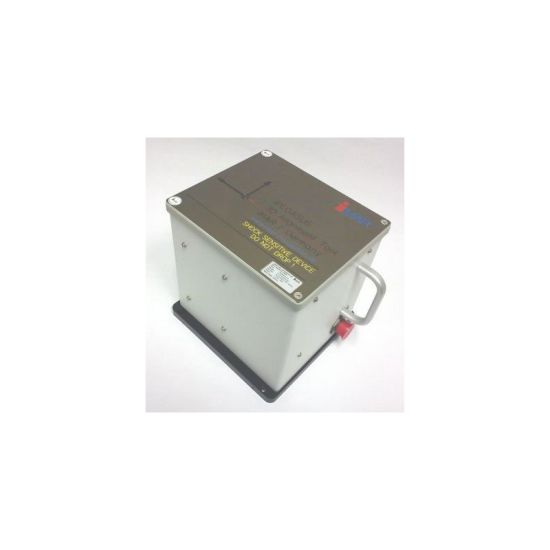
iPEGASUS
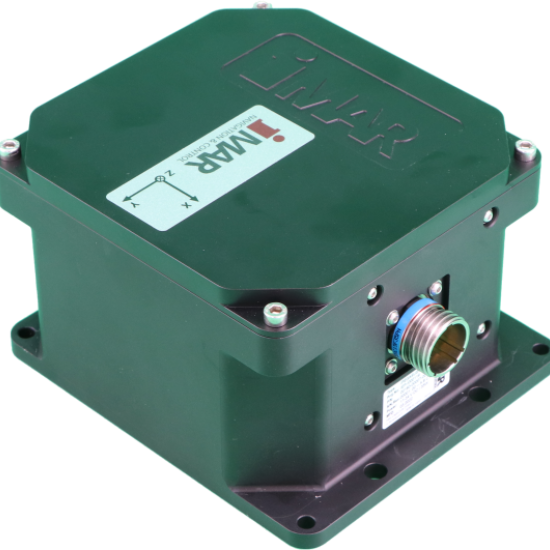
iPEGASUS
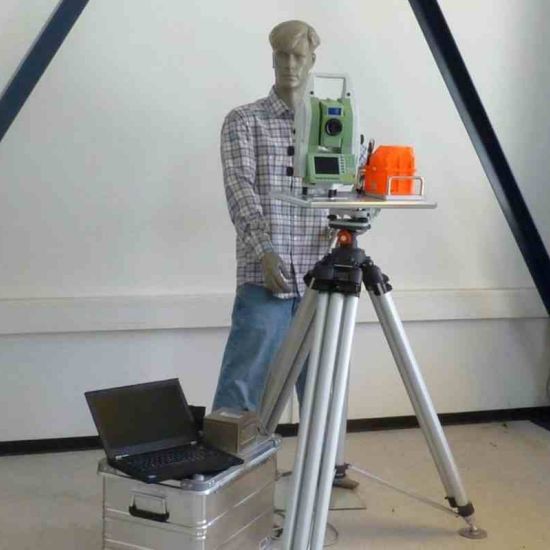
iPEGASUS
Gyro based Total Station Alignment Systems with iPEGASUS Transfer Alignment System
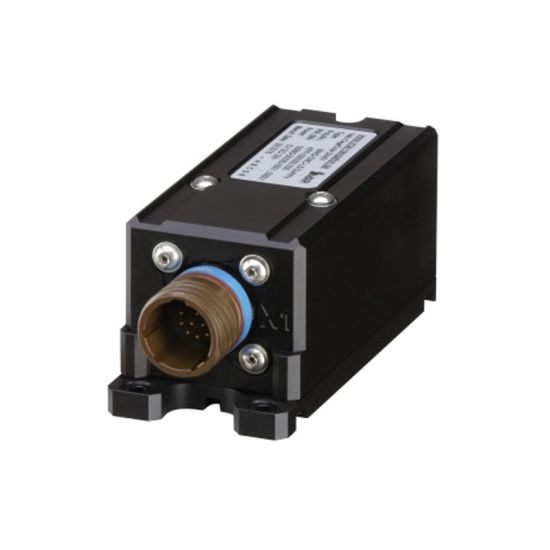
iMAG and iTAHS
Precise Magnetometers without (iMAG) and with (iTAHS) integrated IMU and sensor data fusion for special applications, e.g. for deep-sea environment.
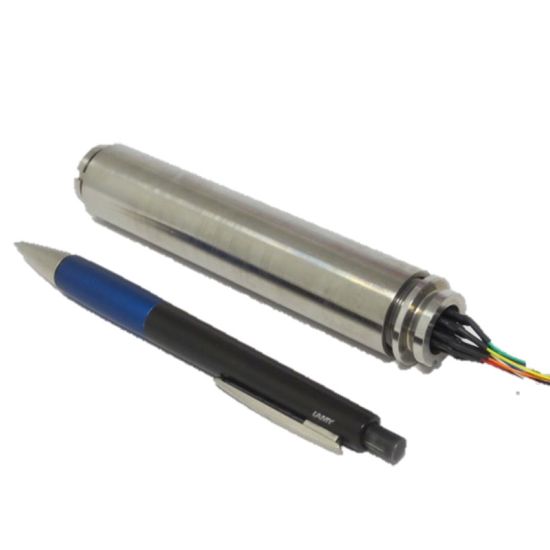
iTAHS
High prerformance magnetometers with integrated IMU, also suitable for subsea applications down to 3000 m depth or custom specific environment.
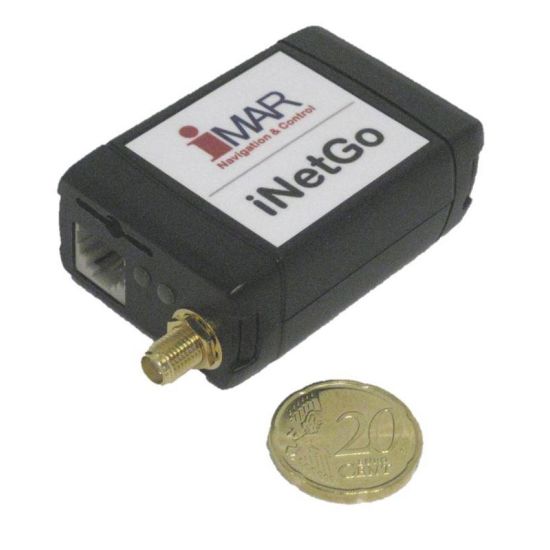
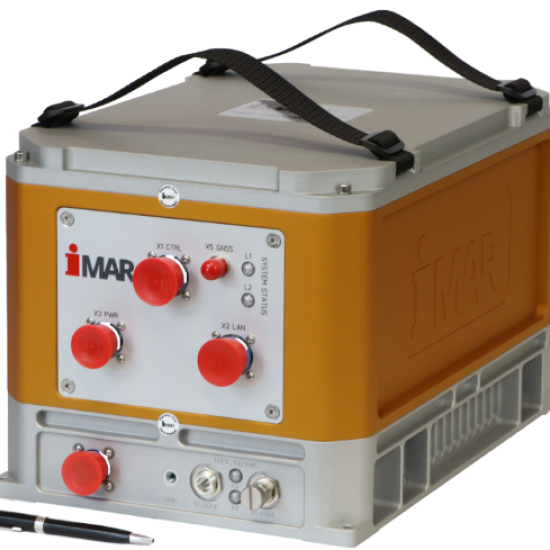
Airborne Gravimeter iCORUS-02
iCORUS is a leading and most suitable strapdown airborne gravimeter for exploration of mineral ressources.
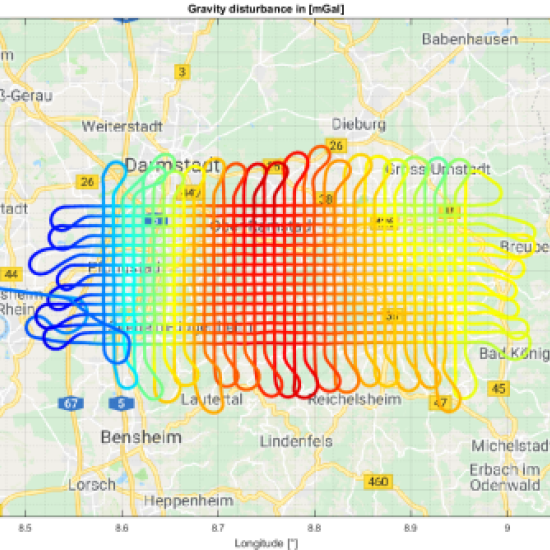
Gravimetry and Post-Processing
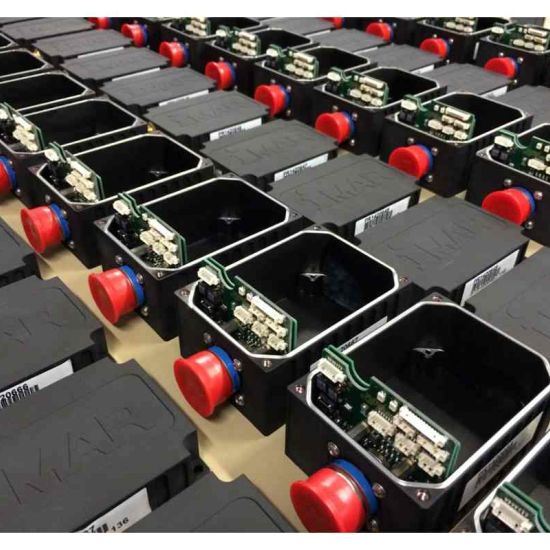
Manufacturing
iMAR is manufacturing according to military, industrial, automotive and aerospace quality standards. The reliability of our products is guaranteed by our modern production site, which is certified according to ISO 9001 / EN 9100 quality standards (industrial engineering / development and production lifecycle according to aviation requirements). The production facility is certified to EASA Part21G (avionics equipment) since 09/2011.
Our production department has the capability to produce according to all needs, from high quantities to single customized prototypes.
Further Information
-
Details about our products and markets can be found here:
-
New products and latest news:
-
Explanations and FAQ regarding Inertial Navigation:
-
List of some of iMAR's customers worldwide:
-
Career @ iMAR Navigation in St. Ingbert:
-
An extended company profile can be downloaded here:
-
What can we do for you today?:
-
Press Releases:
-
YouTube Channel (exciting iMAR videos):
Our discerning, experienced customers have trusted our expertise and solutions for over 30 years:
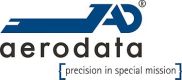
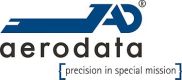




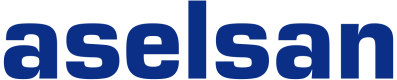
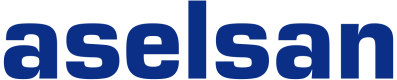
-a3a36730.png)
-a3a36730.png)
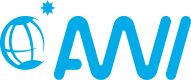
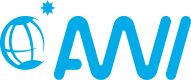
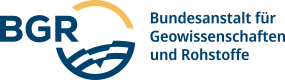
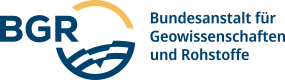
.svg-88e0e112.png)
.svg-88e0e112.png)
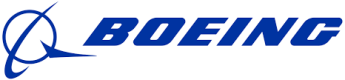
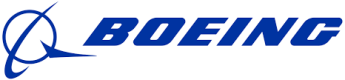
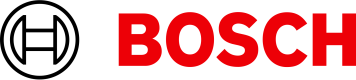
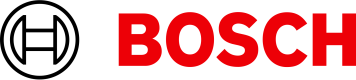
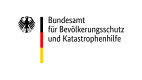
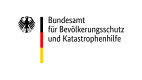
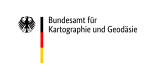
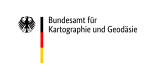




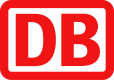
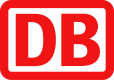
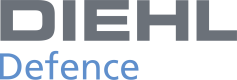
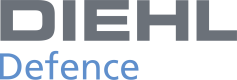


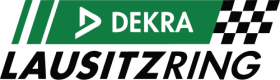
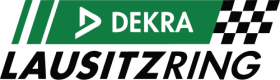




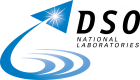
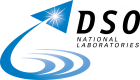
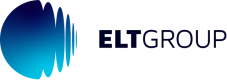
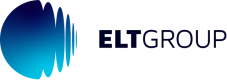
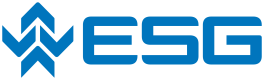
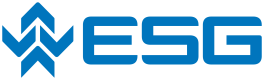


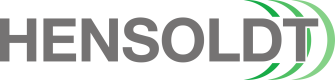
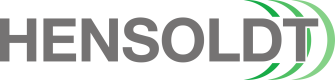
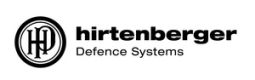
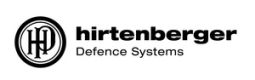
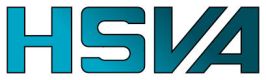
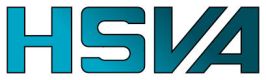
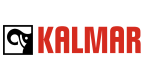
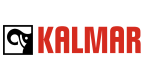
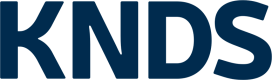
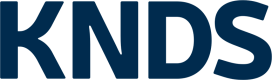


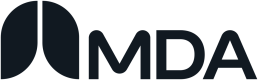
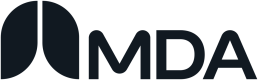
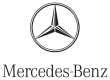
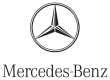
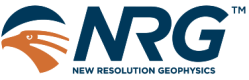
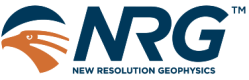
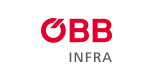
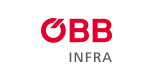
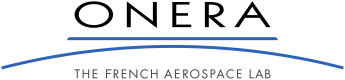
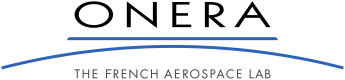


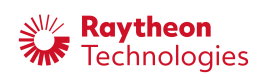
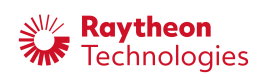
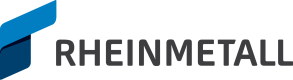
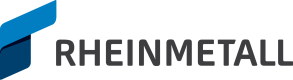


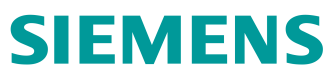
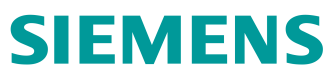
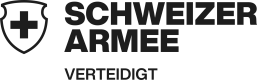
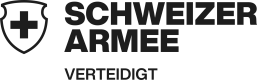
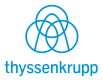
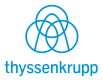




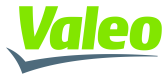
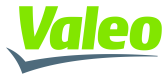


















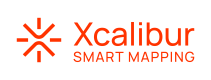
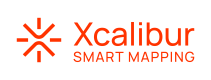
Note: The displayed logos are under the copyright of our customers. This representation is a small excerpt from our client list, which includes over 300 clients worldwide.